The benefits of Value Analysis Value Engineering in the design process
Value Analysis / Value Engineering (VAVE) has the potential to realize cost savings of an average of 10 percent. But what exactly is VAVE? And how can a company apply this methodology?
By: Dimitri Reijerman
Hein de Jong from Value FM will be present together with his partner Timme Hendriksen give a presentation during the WoTS about what the VAVE design method can mean for companies. But first of all, of course, the question: what exactly is VAVE? De Jong: ““VAVE is a structured design method. This method ensures that you design solutions that perform well and do not cost much.”
Then De Jong becomes more specific: “VAVE is a beautifully structured design process, with seven, eight or nine steps. It comes down to first looking carefully and then doing. It is amazing how often that is not done. You see a problem and a solution immediately comes to mind. Jumping to conclusions often works well, because you know what is intuitively good for you. But sometimes you are exhausted, and then what? Then you need a different design method. Then you can think of system engineering, in our eyes the mother of all design processes. And then VAVE is a special method within system engineering.”
VAVEBrainstorming in the pressure cooker
VAVE sessions are short-term studies in which all relevant stakeholders are included. This often involves people outside a company. Think of customers who have their say in this 'pressure cooker'. During the sessions, a function analysis and a cost analysis are made. "VAVE makes designs clearer with good analysis options and insightful diagrams. Once you have done all that, you gain a great deal of insight and overview," says De Jong.
In an interesting case Value FM was involved in, they looked at the construction of a new metal machine at a small, traditional company. “As a small company, you don’t have the real R&D capabilities. But you can bundle all your strengths and sit in a pressure cooker with 5 to 15 people. It’s 50 minutes of asking questions, 5 minutes of coming up with solutions. If you’ve made the necessary function diagrams, you can make a lot of alternative designs in 10 minutes.”
Significant cost savings
VAVE, a concept that originated in the US shortly after the Second World War, is popular in Germany, for example, as Wertanalyse. According to De Jong, the methodology is still relatively rarely used in the Netherlands: “That is strange, because you can achieve an average of 10 percent cost reduction. That figure is based on worldwide studies. Every design that has not been through the mill before can be 10 percent cheaper. If you have sufficient turnover from a product, it is therefore worthwhile to have a VAVE session on it. Because the costs are often in matters that have little added value.”
De Jong and his colleague are busy putting VAVE on the map with Value FM: “We provide training and facilitate the start of a VAVE process at companies, including those in the metal, aircraft, defense and automotive sectors. ASML and Philips speak their own VAVE dialect. We also work with American and English companies.”
Looking at the upcoming presentation at WoTS, De Jong wants to highlight the potential benefits of VAVE together with Timme Hendriksen using a few practical examples and exercises. “Because as a CEO you have to do a lot to get things moving. With VAVE you delegate more of that,” De Jong concludes.
Related companies
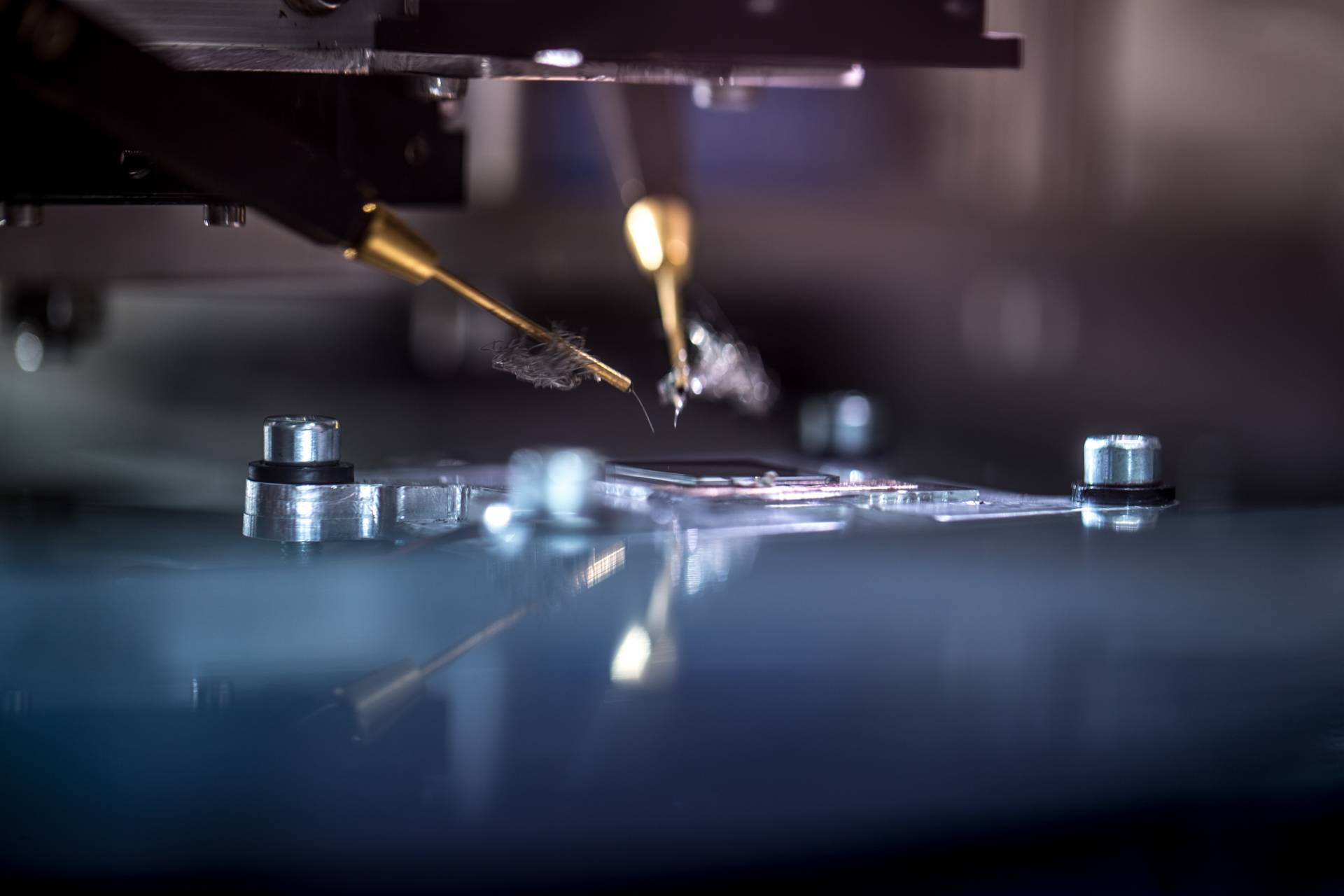