Disruptive mobile robots powered by Elmo servo drives have revolutionized warehouse management
About two decades ago, customers who bought online would wait five to 10 days for their orders unless they paid an exorbitant fee for express delivery. Today, consumers count on instant gratification thanks to e-commerce models. They can download books, music, films and podcasts by tapping on a screen. Even when they order physical products online, they expect to receive their packages in a fraction of the time that was once typical. To reliably provide fast delivery at minimal cost, an Asian e-commerce giant introduced an initiative to replace conventional shipping centers with fully automated, unmanned fulfillment centers. At the heart of the company's success was a low-profile fleet powered by compact, efficient, powerful servo drives from Elmo Motion Control.
Compact mobile robots
This retail business sells a wide range of goods ranging from seafood to shampoo, T-shirts to tablets, and much more. To meet customer demand, the sorting centers must be able to process 9,000 packages per hour. The solution was to place the stock in containers that are transported through the warehouse via mobile robots. The holders stand on metal legs. The robots roll underneath and go straight up until the legs clear the floor (see image). Now the robot can drive the container to a target packing station, navigating via barcodes placed on the floor of the logistics center.
This type of warehouse management presents us with a number of challenges. The robots must have a low profile so that they fit under the holders. They must also be as compact as possible so that hundreds or even thousands of them can move through the complex without collisions. At the same time, they must be able to lift heavy loads, with one container holding tissues and the next holding bags of 300kg of dog food. Finally, the robots must have the longest possible battery life. After all, the warehouse cannot respond to customer orders if all robots are connected to the charger.
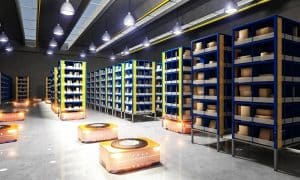
High power density
The robots are driven by two wheels. They also have vertical lifting capacity to lift the holders. To drive the two wheels, the designers incorporated two 750 W brushless servo motors. Given the space limitations in the robots, the team needed drives with the highest possible power density. They found the system solution in Elmo's Solo Guitar drives. Solo Guitar drives deliver 4.8 kW continuous power or up to 5.4 kW peak power, at a size of just 46.7 mm x 61 mm x 80 mm.
The third axis in the system is the rotary lift that can lift up to 300 kg and is powered by a 100 W brush motor. For this axle, the team chose an Elmo Solo Whistle drive, which has both a continuous and peak power of 2 kW, with a size of 58.25 mm x 46.5 mm x 28.5 mm. The Solo Whistle drives receive pulse/navigation signals directly from the customer's control system.
High-efficiency drives
The battery life of a mobile robot is highly dependent on the efficiency of its electrical components. The more efficient the servo drives, the longer robots can operate between charges. The Solo Guitar drives have greater than 97% efficiency, while the Solo Whistle drives have greater than 99% efficiency. This makes them ideal for working with limited power supplies and extends the robot's overall duty cycle.
The power characteristic of batteries varies per discharge cycle, but also during the entire life of the battery. Solo Guitar drives are designed to handle voltage fluctuations between 46 and 195 VDC, while Solo Whistle drives can handle voltage fluctuations between 12 and 95 VDC for the 100 V unit and between 24 and 195 VDC for the 200 V unit. As a result, they minimize unnecessary disruptions and can guarantee continuous operation.
Minimizing timing errors and delays
To control robots, the drive shafts must be precisely synchronized. The design is based on a master-slave architecture where the primary axis receives commands from a customer-designed control system via an analog ±10 V command. For feedback, the axes use a combination of Hall effect sensors and a 1000-line incremental optical encoder. The design team initially planned to control the synchronization analogously. However, the Elmo drives offered a more effective alternative.
Elmo drives can receive or generate a wide variety of reference commands: analog ±10 V, pulse width modulation (PWM), pulse/direction, encoder follower, ECAM, user program and direct communications. In the case of the warehouse robots, the drives were controlled in PCM mode. Elmo drives allow PCM commands to be used as current reference commands or as speed reference commands, all of which can be easily applied with readily available Elmo utilities. This allows the robot drive system to send a high-speed PCM command from the primary to the secondary drive shaft. PCM synchronization to a slave is an ideal way to achieve shaft following with minimal timing errors or delay. The PCM synchronization proved to be much more successful than the original analog control concept.
So far the project is working well. After two months of testing, the performance and overall functionality of the drives meet requirements. In the next generation of robots, communication will be conducted over a CANopen signal instead of an analog ±10 V signal. With the addition of Elmo's full CANopen support, flexibility in drive programming and a wide voltage range, this vendor has acquired the ideal servo drive system for its growing warehouse robot base.
The initiative is now moving into the production phase, with an expected 1,000 robots over the next three to four years for the planned 10 unmanned sorting centers. The e-commerce giant wants to continue investing in innovative technologies for highly efficient, low-cost and intelligent system solutions in the supply chain.
