Efficient working is everywhere hot topic. This also applies to the laboratory sector. How do we improve the quality of work, deploy employees optimally and create a smart workflow? All kinds of questions that are often asked in the lab today.
René van Bergen, sales manager laboratory instruments Netherlands at METTLER TOLEDO, shares his view on what we call lean lab. He is trained as a laboratory analyst, has years of experience in the industry and is a fan of the lean trend. You can read what the lean lab is and how it works here.
What is a lean lab?
René: “In short: you organize your lab in a way that processes run optimally. In practice this is different for every lab. You look at time, costs and quality.” The combination of the three determines efficiency.
A requirement is that you look critically at your workflow. “That is often the first hurdle you have to overcome. In many laboratories, work has often been done in a certain way for a long time. It is then difficult to break those fixed patterns. To do this you first have to use a open mind dare to look at your processes.”
“The work is still often based on traditional approaches and standards that were established in the past. Now it is time to revise it.” – Rene
Getting started lean
You can't build a lean lab in one day. “The first step is to look at the work processes,” says René. “Just like with an audit, you ask employees how they do their daily work.” You are not critical of the people, but rather of the processes that are carried out.
“Based on those conversations, you identify the challenges and priorities that you want to make lean first. You cannot make the entire lab lean at once, but work in steps.”
Steps to a lean lab:
Talk about current work processes. Determine priorities: what do we make lean first? Take an inventory of supplies. Start with 'verleanen'.
The most common challenges
René: “Pen and paper are still popular. I'm always amazed by that.” It is human nature to pick up a pen when you want to write something down, but nowadays it is almost old-fashioned. Equipment in labs is increasingly being replaced by computers that automatically process data. According to René, this has many advantages: “It is more accurate. Laboratory equipment is self-learning and is therefore becoming increasingly precise and faster. If these systems are linked to specific software, making your lab lean becomes really fun. And correctly registering, processing and reporting analysis data is also becoming increasingly important.”
He also sees that there are still many people moving around the laboratory. “You actually want the sample to move through the lab, not the lab technician.” Based on the lean philosophy, people often stay in one place while the work moves around them. René: “Samples are often grouped, but it is much more efficient to have one one piece flow to adhere.” That sounds contradictory, but in practice it saves a lot of time: you need fewer steps to carry out the workflow.
Benefits of lean lab:
- lower cost per analysis;
- process more analyzes with the same number of people;
- reduction of the number of steps in the workflow;
- insight into personnel planning, i.e. into growth opportunities and optimization of capacity;
- higher quality through more efficient processes.
Automation is inevitable
When you say lean lab, you say automation. René: “If you write out how the processes run, you can see what hardware is actually needed to do it more efficiently. Automation is often the logical step.” As a sales manager at METTLER TOLEDO, a supplier of precision instruments and services for laboratories and production environments, he sees this development reflected in his work every day. “We also challenge the customer in this and ask the customer as standard: how are you going to organize this process effectively? Based on the answer, we then recommend equipment and materials that contribute to a lean approach.”
Lean lab: not a trend, but the future
If you ask René, lean is certainly not a trend, but the future. And he sees even more developments in the industry: “The demand for automatic data reporting is increasing. Hardware is still important, but so is software. With dashboards, BI reports and ERP systems, it is becoming increasingly complex, but also more efficient.” We are also increasingly seeing the linking of analysis data to production management systems because the analysis data then guides the management of production processes.
Another trend he sees emerging is the use of artificial intelligence (AI) in the laboratory. René: “Using algorithms, the computer then predicts the outcome, so that processes in the laboratory are organized more efficiently, with higher delivery reliability and even better quality. For example, that saves a lot of reanalyses and costs.”
Related companies
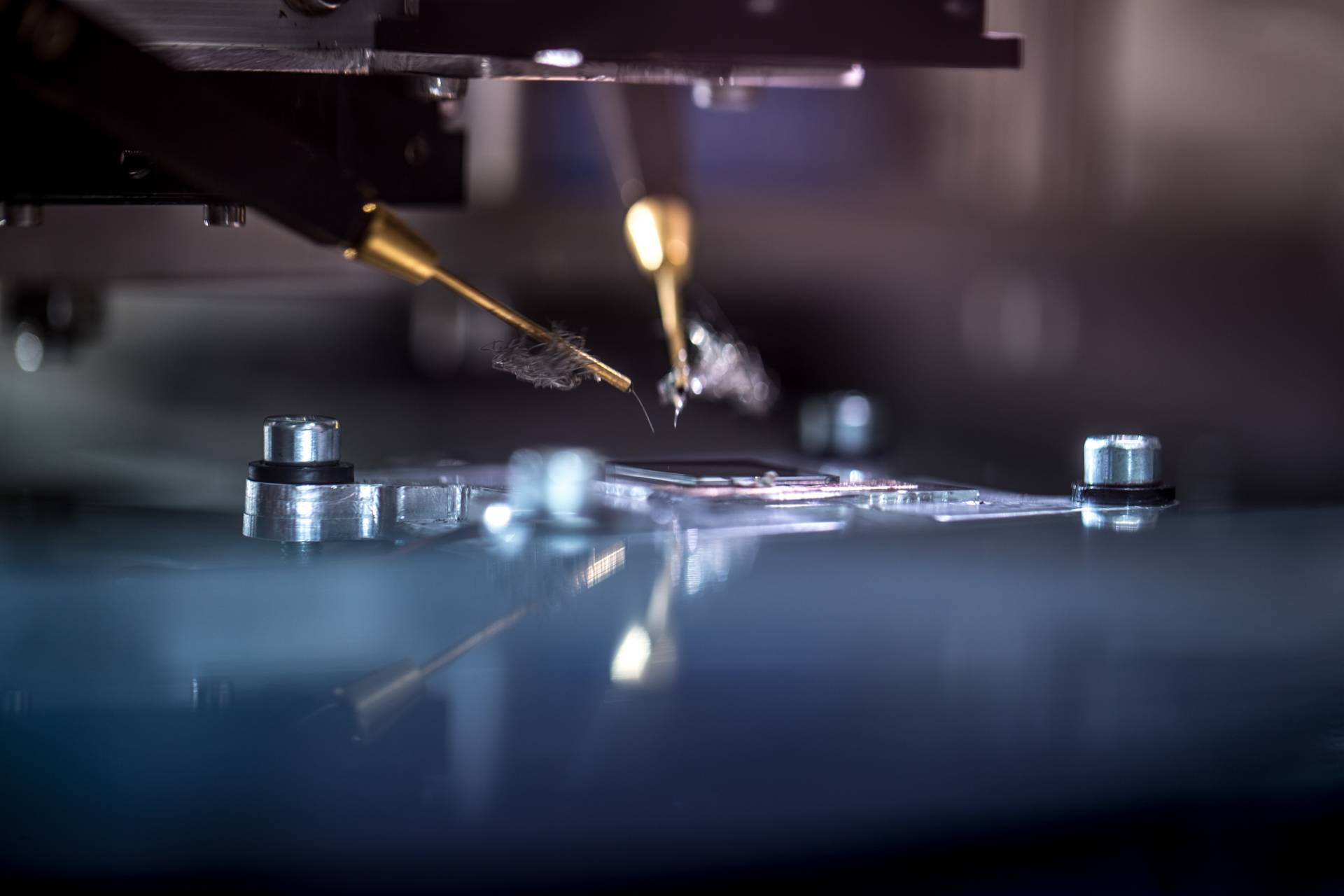
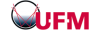
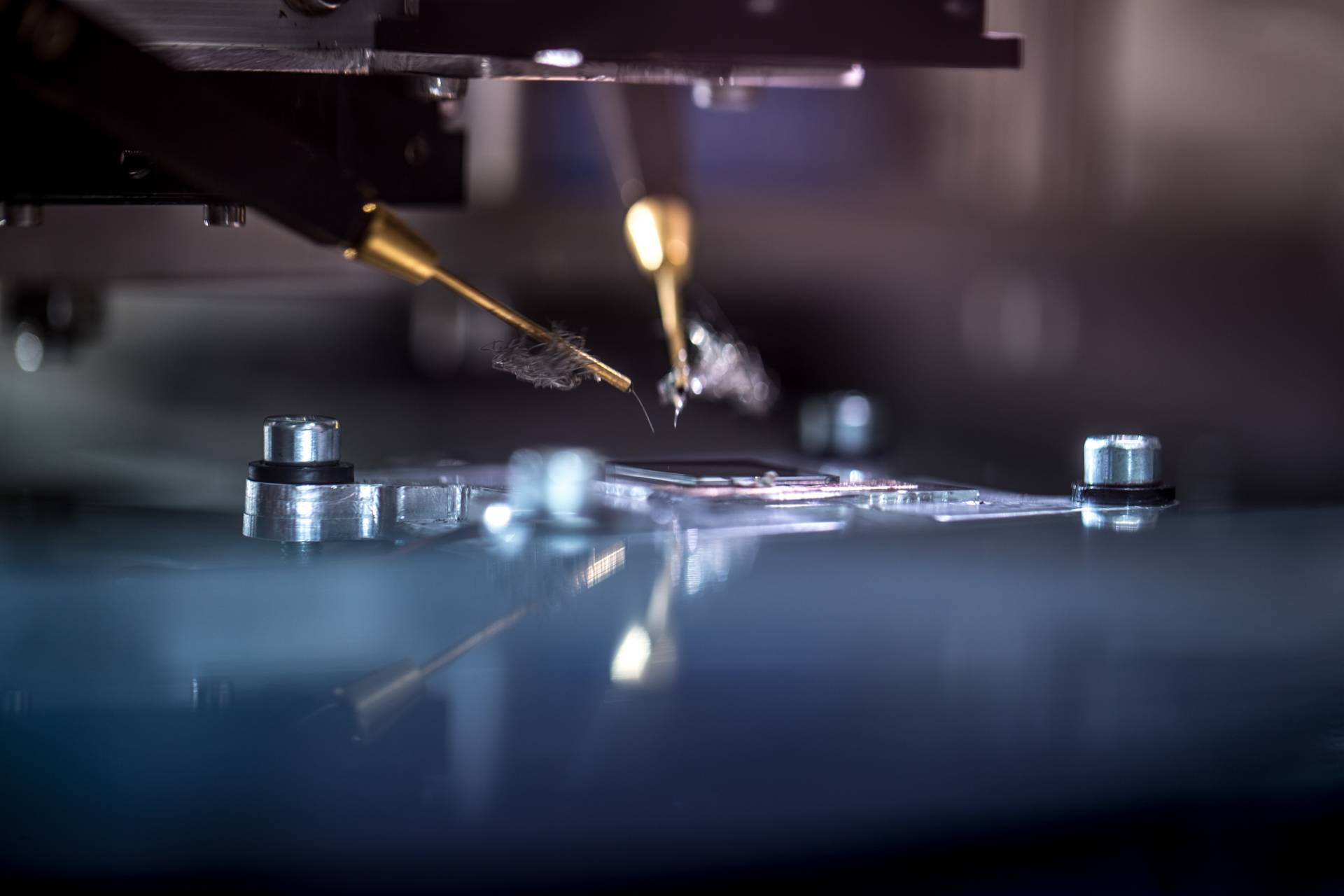