The development process of Hardware Design: from creative idea to working concept
You've probably experienced it: you have a fantastic idea, your colleagues respond enthusiastically and all think you should do something with it. You make a plan full of energy, but then... Where do you start? How do you approach it? Before you know it, six months have passed and everyone (including you) has forgotten about your fantastic idea. The story of your life? Then the presentation is over Jeroen Rondeel of Blue Engineering during the Hardware Design seminar recommended.
The Venlos engineer and entrepreneur will speak on September 29 during the WoTS about the development process of a new product. Using a concrete example, the plasma generator 'Blue Plasma', he describes the steps his company Blue Engineering takes to move from a creative brainstorming session to a validated prototype and end product.
Rondeel knows what he is talking about, because he and his colleagues were involved in the development of dozens of new products. Usually on behalf of customers, but sometimes also on our own initiative. One of the most recent innovations of our own making is a device that reduces harmful nitrogen emissions to zero. “I deliberately use the Blue Plasma as an example because we use this device from scratch have devised and developed,” says Rondeel enthusiastically.
“The reason for the development was the revolutionary discovery by scientists from Eindhoven University of Technology about the bactericidal and virus-killing effect of plasma (another name for lightning). We wondered whether we could also apply this principle to nitrogen. That turned out to be the case. This is how our 'product creation journey' began; as a creative idea during a meeting”.
The essence is central“I have learned through trial and error how important it is to focus on the essence from the start of a product creation process. Which functions are really necessary for the functioning of the product (critical-to-quality) and what are the bells and whistles. By clarifying this at the drawing board, you avoid getting bogged down in conversations about specs that are nice, but that have no added value. Before you know it, you're wasting hours on designs that you never end up using.”
“That is why we invite one in the first phase of the process industrial engineering partner to think along with us. They know exactly what is and is not possible during the production phase. You can think of anything, but if it is ultimately not feasible, you have invested all that time and effort for nothing.”
Modular working
“A second way to save time and effort is to work modularly. Where possible, we use existing technologies so that we know more quickly whether a device is functioning as intended. For the Blue Plasma, for example, it is very important that the power has low noise. The power electronics must operate stably in a precise processwindow. This is essential for quality. That is why we started looking for existing power electronics that meet these strict quality requirements during the design phase. This way we don't have to reinvent the wheel. Ultimately, our engineers developed a control mechanism that allows us to make plasma work very reliably. We have a patent on that. It is better to spend a few euros more on electronics that work stably than to check and correct afterwards.”
“It is better to spend a few euros more on electronics that work stably than to check and correct afterwards.”
“Each product contains components that are more vulnerable, for example because they are often used and therefore wear out faster. If you know this, you can do two things: either you accept that the end product has a shorter lifespan or you invest in a high-quality component that far exceeds the critical time limit. We choose the latter. It improves product reliability and ultimately our customers want this too.”
Dare
“We think sustainability is very important. That is why we always use an aging test to see how a product will function in 10 or 15 years. You have to dare to do that, but in the end you will save costs. By tackling the hardware design properly right from the start, you will produce the components in an industrial manner. You limit error rates during production and therefore reduce production costs.”
“During the lecture on Hardware Design I will tell you more about the development process itself,” Rondeel concludes. “Taxpayers who want to know more about our innovations are very welcome at our stand DevelopmentClub/IoT pavilion, number 9B076.”
Knowing more?
During the Hardware Design seminar at the WoTS fair, on September 29 in the Jaarbeurs in Utrecht, Rondeel will tell you more about Blue Engineering's hardware design process. Rondeel kicks off at 9:30 am. Admission to the fair and the lecture is free, but you must register in advance register.
Related companies
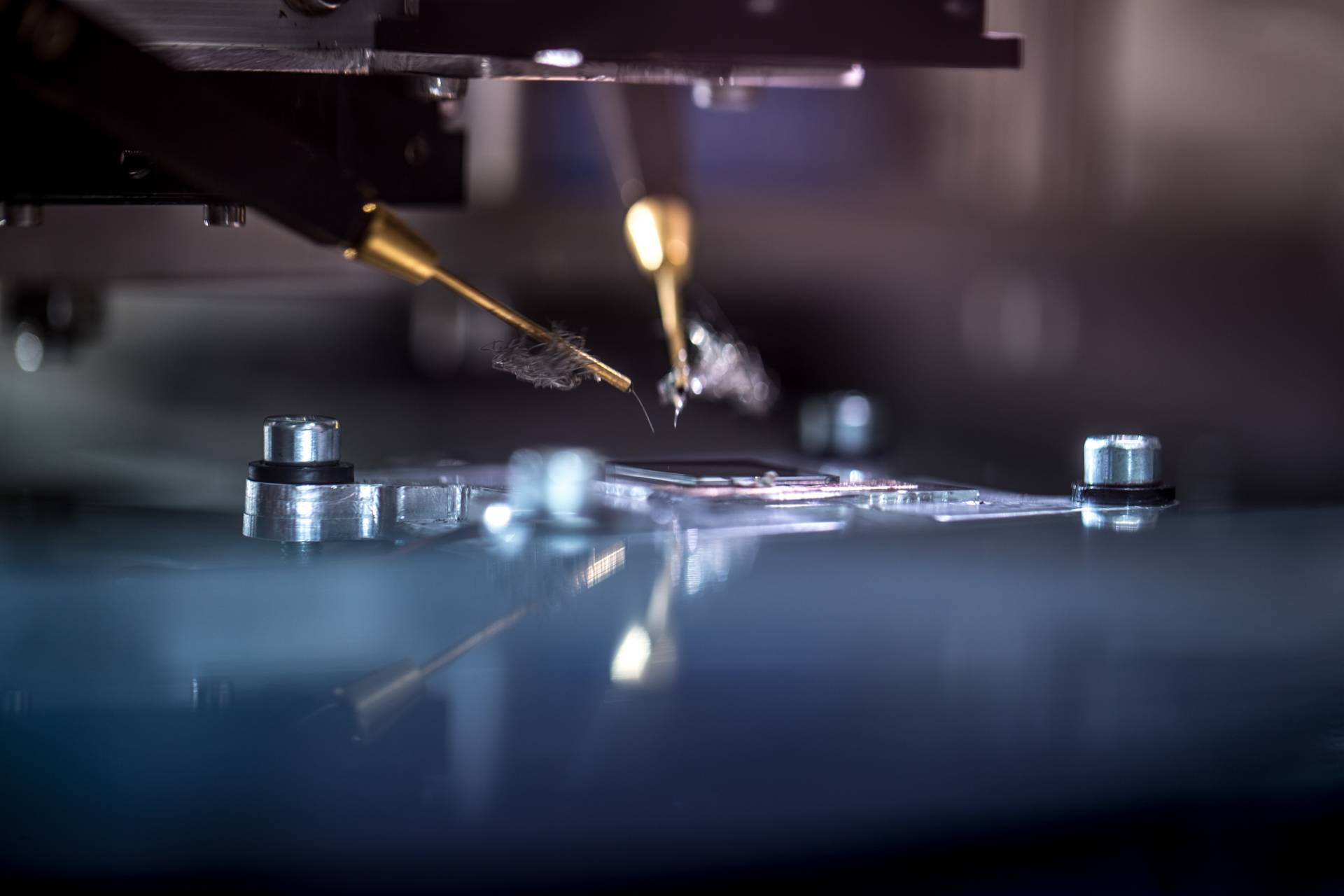
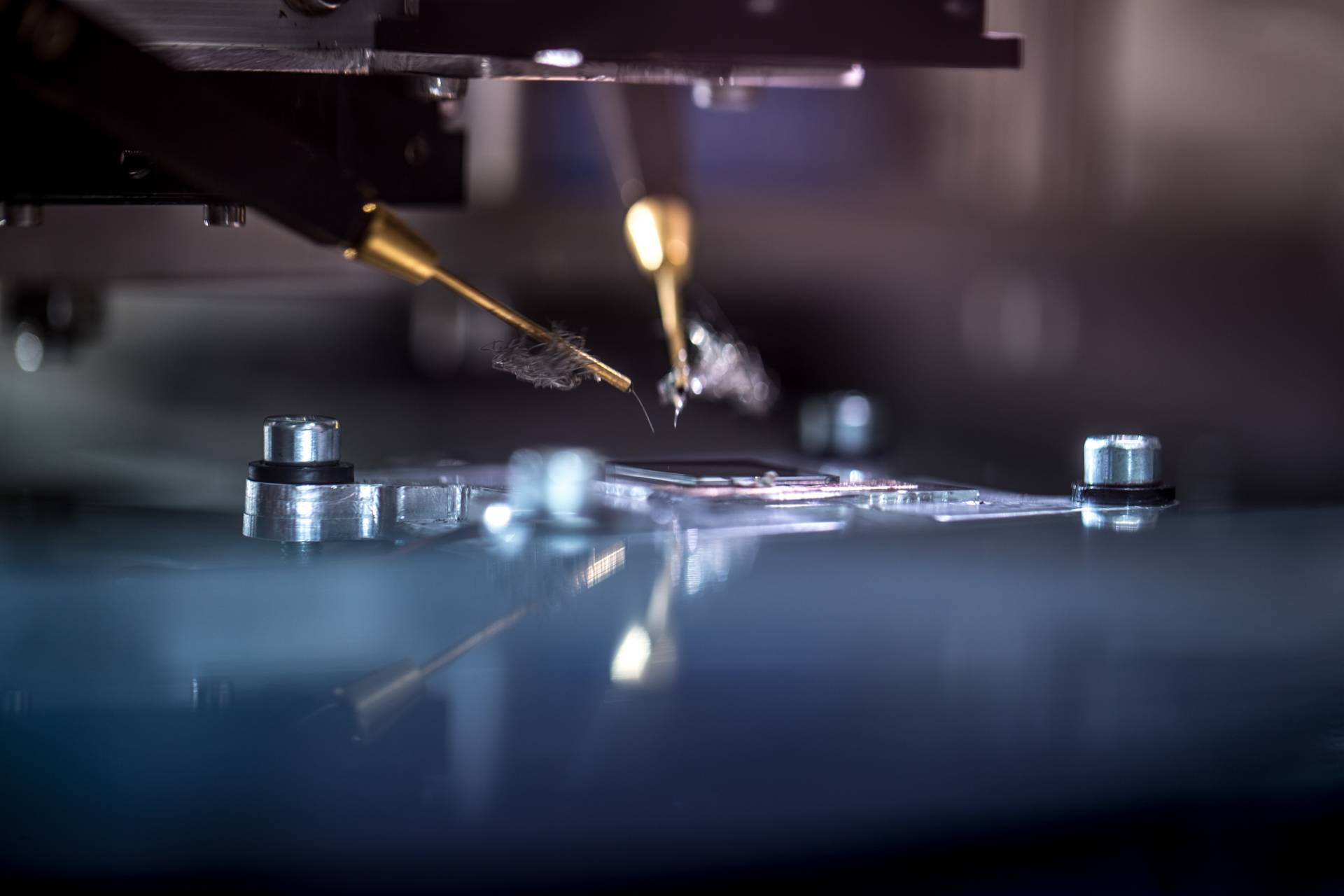