OperationAIR: develop a ventilator from scratch
During the first corona wave in March of this year, OperationAIR, a student team from TU Delft, managed to cause a stir by developing a functioning emergency ventilator in seven weeks. Hubald Verzijl was closely involved in the development and tells during the online Medical Electronics event about his experiences in this hectic period full of improvisation and ingenuity. We spoke to him in advance.
By: Dimitri Reijerman
Verzijl is doing a master's degree in mechanical engineering, but is also following the master's degree in Technical Medicine, a program that has only existed for a few years. Verzijl was doing an internship when the coronavirus took hold of the Netherlands at the beginning of this year and daily life largely came to a standstill in March. It was a crisis. "Suddenly all the hospitals were full," says Verzijl, looking back. "All internships were cancelled and suddenly we were all at home. Then the director of our program came and said: there could be a serious shortage of ventilators, let's see if we can develop something. That's when the OperationAir project started rolling."
Especially the initial phase of the hastily constructed OperationAir project was challenging, says Verzijl: “You suddenly come together as a group of students with the big question: how are we going to tackle this? Normally you already have a team leader who sets out the guidelines, but that was not there yet. That is why we spent the first week mainly working on getting the internal logistics right. We eventually set up three different groups: a design group for the device, but also a group that studied predictions in the field of corona. Because will the predictions for a shortage come true? And a management group was created to manage everyone and provide continuous updates. They also made the connections with the media and with people who wanted to help us.”
Complex machinery
Developing a ventilator from scratch is far from simple, says Verzijl: “If you take a ventilator apart, you will see that it is quite advanced. And that is a good thing, because a lot of attention is paid to patient safety in the design. A standard ventilator can also do much more than ventilate a corona lung. So the question for us was: what should our device meet in order to ventilate a corona patient, because you have to use a different method of ventilation for such patients. You need a higher pressure and also a higher level of oxygen. Ultimately, we also looked at which parts we could leave out.”
The OperationAir team could get to work after the specifications were determined. The tasks were further divided: “A medical electronics student is not going to design the printed circuit boards. You let someone who does electrical engineering do that. And that way you also look at the right person for aspects such as safety, the user interface and user-friendliness.”
“Within a month we had a working concept on the table: the AIRone,” says Verzijl with some pride. “That was still a makeshift design, but from that moment on things went fast. Because the basic idea of the design was also that it would be easy to produce. For example, all components had to be easily available.”
Design is open source
In the spring of 2020, the Ministry of Health, Welfare and Sport seized all options to prevent an impending shortage of ventilators. “For example, they worked on concepts in which two patients were connected to a ventilator. But we were also well sponsored because VWS said: go ahead, we may still need you. The requirements for such a device were temporarily lower at the time, because we were in a kind of war situation.”
Ultimately, the emergency scenario did not materialize. “After that, of course, the requirements quickly became higher again, which is only a good thing. We had finally developed a working device, but not one that meets all the requirements of a normal ventilator.”
The OperationAir team took an open-source approach to designing the AIRone. All technical details about the machine are can be found online. With this, the OperationAIR team also hopes to help countries where there is still a shortage of ventilators. “Quite a lot of people wanted more information about our design,” says Verzijl. “We learned from that. But so did others. For example, they can check what the maximum ventilation frequency should be, or the maximum amount of air that someone can take in per breath.”
Lessons from practice
Verzijl learned a lot with the OperationAIR project: “My hobby is also electronics and my desk is always full of printed circuit boards. And there you see an oscilloscope. So I really enjoyed seeing how we were able to use everyone's quality to come to an end product.”
He continues: “I also learned a lot about the steps needed between prototype and production. The government eventually bought eighty of our devices. The goal was for us to learn how scaling up works in practice. If more ventilators are needed later, we already have the necessary experience. We set up a production line for this together with assembly company Applikon. This teaches you that you have to take the aspect of scaling up into account during the design process.
And he also remembers the challenges in the technical design: “We once sat at DARE!! for EMC tests. At first we got shocks from the device and when we turned on the antenna of DARE!! the screen started to flash. Then there were some more challenges to solve. Fortunately, with some aluminum tape it went a lot better.”
Would you like to attend this lecture? Register for free on the website of Medical Electronics.
Related companies
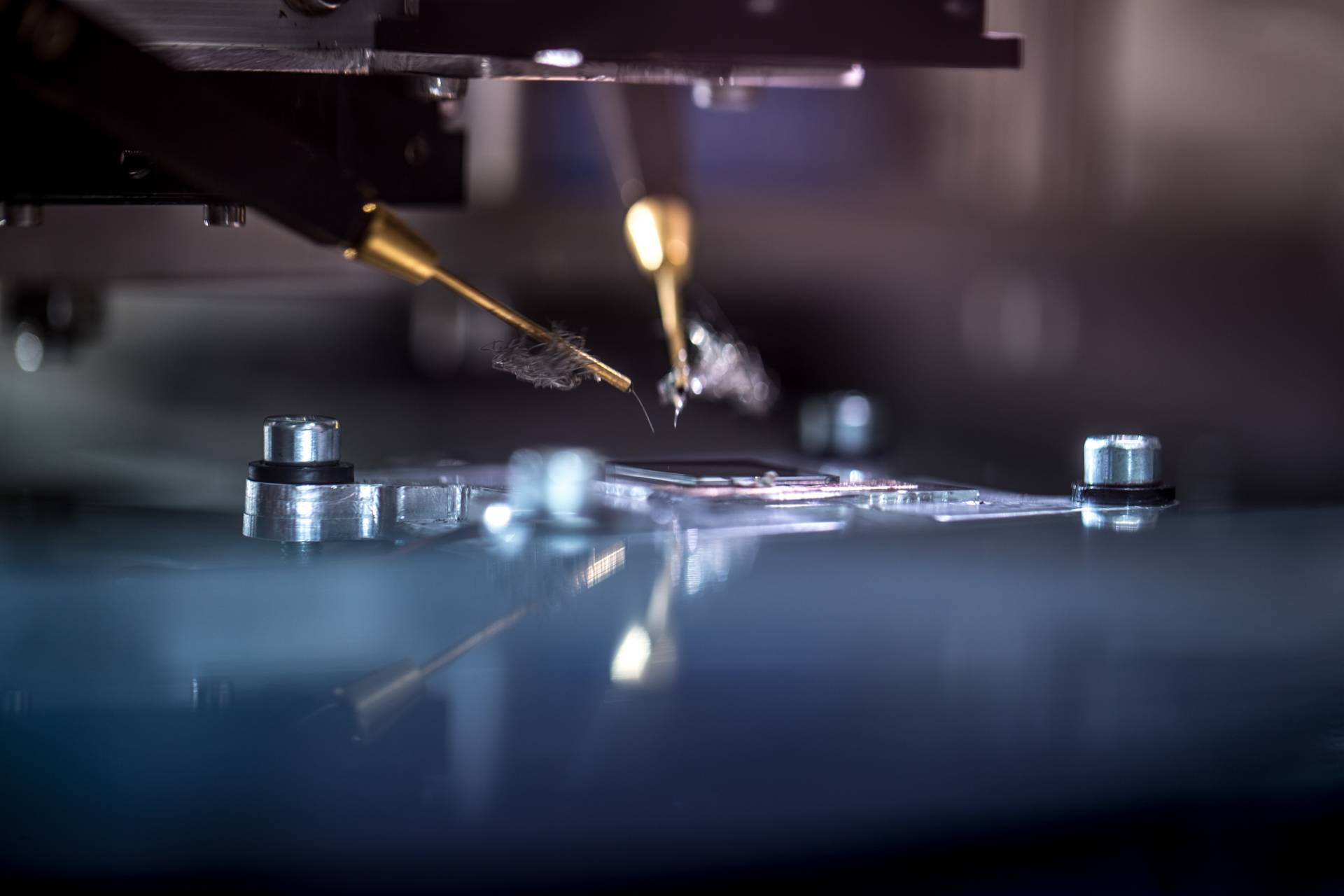
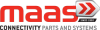
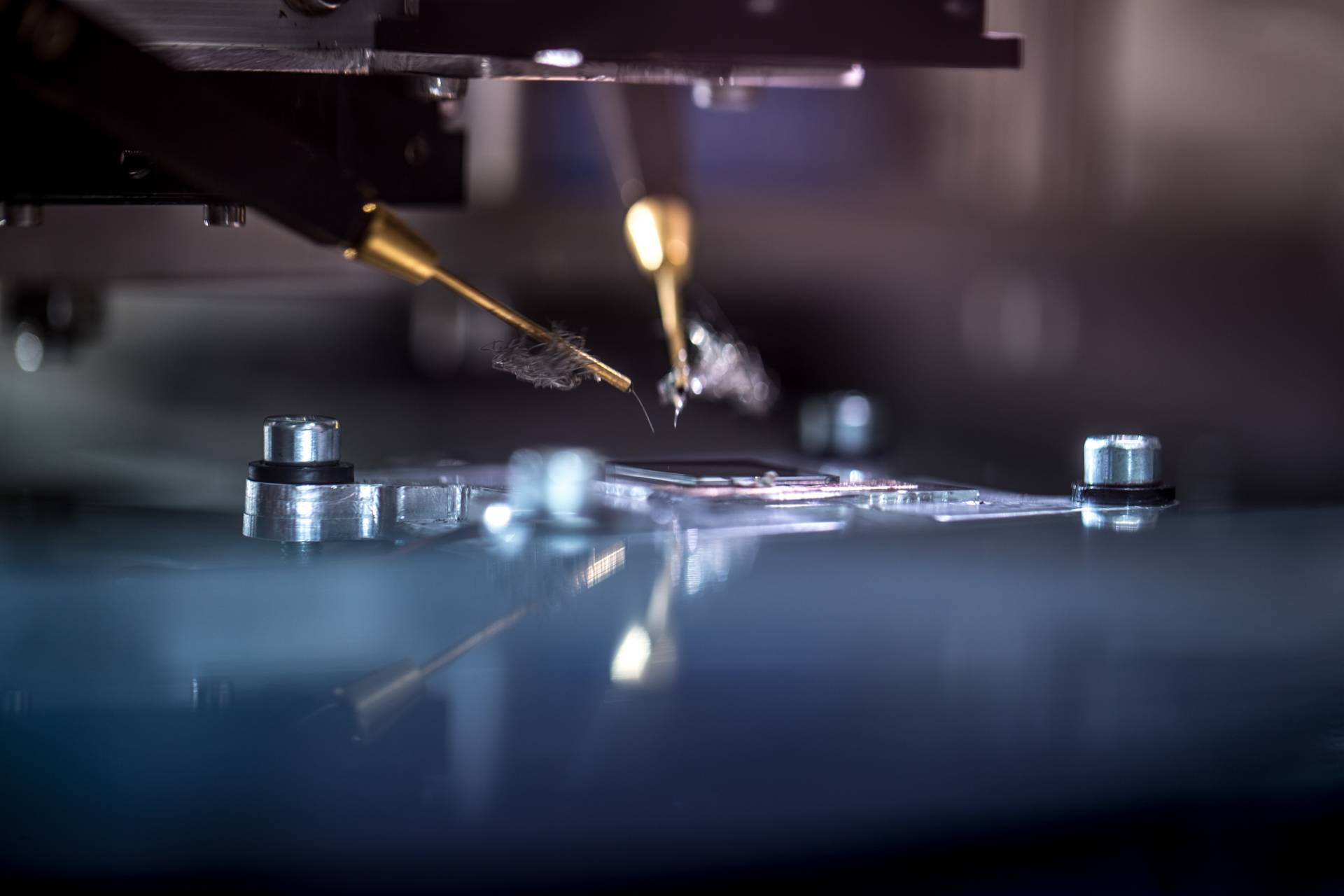
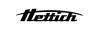