“We are far too dependent on foreign countries for materials”
Better communication within the industrial electronics sector can prevent a lot of problems and irritation between buyer and seller. The political The Hague can also play a more active role in tackling the problems of material shortages, supply problems and component shortages within the sectors. The arrival of factories that produce scarce components, for example, is a good first step. Stimulating employment within the industrial electronics sector is also advisable. These are some of the conclusions from the consultation between the clusters Components and EMS, part of the Industrial Electronics sector of FHI.
FHI invited the Components and EMS clusters to discuss common problems. The Components cluster manufactures the materials that the EMS cluster in turn needs. However, both parties are faced with unclear delivery times, material shortages and price increases.
The aim of the cluster meeting was to learn from each other and to gain insight into bottlenecks. Using a number of questions, an attempt was made to map out the biggest problems. What is considered the biggest problem: material shortages, component shortages, delivery times or something else? There was no clear answer from the clusters, because it concerns a combination of circumstances. Stock shortages, material shortages and incomplete communication: this combination of problems is called the perfect storm.
Technologies such as e-mobility and the 5G network are gaining momentum and this has consequences for the manufacturing industry. As there is more interest in these industries, the demand for materials has increased. “This large increase has created scarcity and this also has an impact on the production of components. This development also results in longer delivery times. All these things are inextricably linked,” says a member of the Component Cluster. Dependent
Only a third of all electronics come from Europe. The number of PCBs is even less. The corona crisis has accelerated this problem. As the demand for electronics increases rapidly, it is striking how dependent the chain is on supplies from Asia. “Our dependence on foreign suppliers is now killing us,” says a member of the EMS cluster. “There has been an implosion in the market. The raw materials for PCBs have to come from Asia. In Asia, they are facing the same problems and that is why the domestic market takes precedence.”
The corona crisis has highlighted a number of pain points when it comes to inventory management.
Due to the pandemic, a number of factories were closed and production came to a complete standstill. Due to a lack of components, equipment was not in stock. At an international level, there was hoarding. For example, some parties adjusted their purchasing policy and bought a lot of stock at once. A band-aid, as it turns out. The bottom of the stock is quickly in sight due to the high demand. Both clusters also had to deal with delayed delivery times, because logistics companies such as DHL and UPS are behind on delivery.
Clarity needed
Due to the corona crisis, people are spending money differently. A holiday is out of the question, so a PlayStation 5 is coming into the house or the purchase of an electric car is on the agenda. “That means that there is a demand for certain components. This requires raw materials that are scarce. Planning is needed to meet the demand. EMS'ers do not want idle machines and component suppliers want to deliver their components but do not have the raw materials for this. Clarity is what is needed. If it is clear what the delivery time is, this is taken into account in the planning,” says a member of the Components cluster.
A solution is needed for the scarcity. A first step is re-shoring. At present, the clusters are largely dependent on foreign manufacturers. By choosing alternative components, the chain can tackle part of the problem. “It is not the first time that this has happened and it certainly will not be the last time. In four years, I bet we will be discussing this theme again. We need to look for solutions instead of focusing on the cause. I think that politicians in The Hague should advocate opening more factories in our country. At present, we are far too dependent on foreign countries. However, the arrival of more factories is not the solution. The demand for components is high and we cannot possibly produce all types to meet the demand. It is all connected,” says a member of the Components cluster.
Alternatives
A possible solution is to look at alternatives with the customer already in the design phase. If a certain material or component is scarce, it is wise to have an alternative ready. “It would be good if designers already think about possible alternatives in the preliminary design”, argues a member of Componenten. “That way you prevent possible problems. The hardware designer should already think about this during the design process. It is too time-consuming to suddenly choose other types of materials or components. Sometimes it takes months before a new design is approved. In that time span, it is possible that the alternative components have already run out.”
Communication between customer and seller is essential and there is much to be gained in this area. “Better communication between customer and supplier is desirable. By communicating faster in the event of delivery problems, you can prevent a lot of frustration. You can communicate quickly via Teams. Better communication is necessary. Providing information is important. It is not a problem if an order is delayed, as long as you are honest and transparent about it. By leaving customers in the dark, you make the situation worse,” explains an EMS member.
Insecure
It is still unclear what the future will bring. These are uncertain times. The shortage of components makes it very difficult for companies to make a plan. “I cannot give customers any clarity and I do not expect any improvement in the short term. Our purchasing department has been expanded to be able to process all order confirmations,” says a member of the Components cluster.
“Electronics have been falling in price since the eighties,” says a member of the Components cluster. “The chain no longer wants stocks, because storing them costs money. Because so many products have been outsourced, we are in a difficult position. By making more items in our own country or in nearby countries, you strengthen your own position. Because we chose to outsource production in low-wage countries, we are now in a difficult position. This is not the first time this has happened. I think we need to make things more sustainable and not opt for dumping prices. However, that means that someone has to dare to take risks.”
Communication
Communication is difficult for both clusters. The Components cluster also struggles with this: “We don’t know when materials will arrive. As a supplier, we are also uncertain. We try to keep our customers informed as best we can. This is not easy due to poor information provision.
Both clusters are very satisfied with the meeting. The two groups listened patiently to each other's positions and findings. Both parties hope that political The Hague will think along about solutions. The cluster consultation is already a good first step to bring parties together. By jointly mapping the pain points and brainstorming possible solutions, a constructive start has been made. FHI plays a connecting role in this and brings parties together.
Related companies
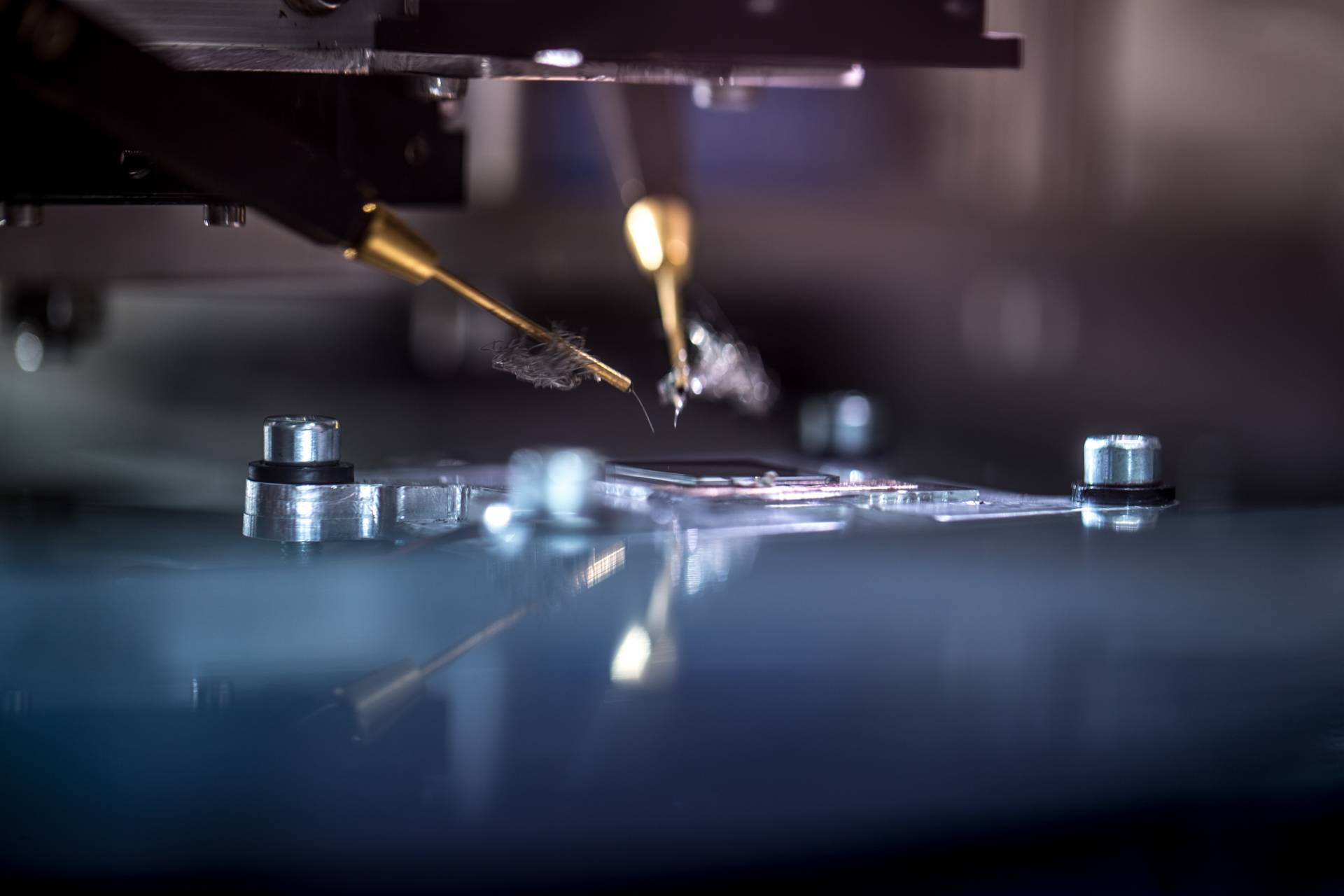
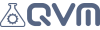
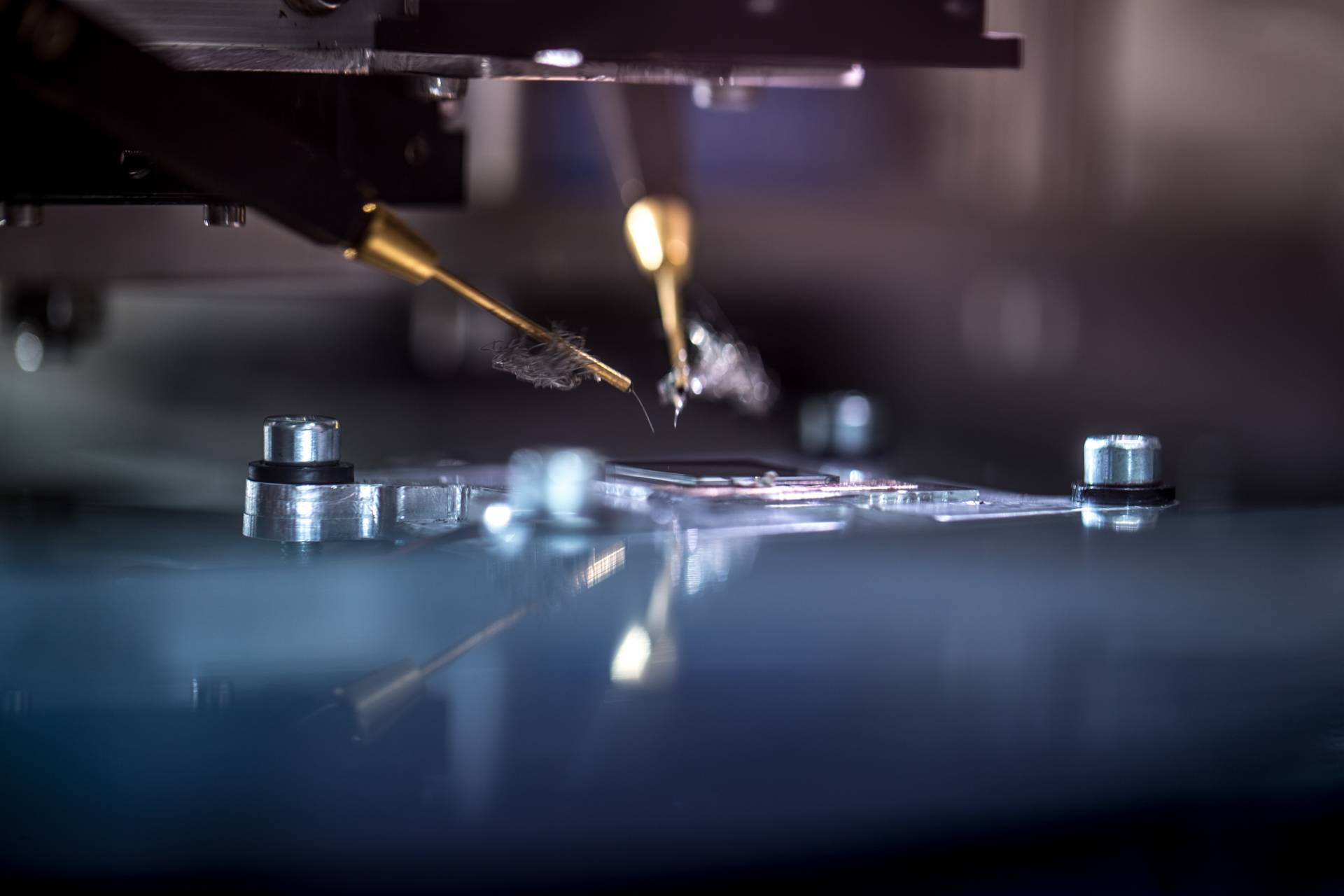
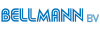