Calibration processes and challenges in a large environmental laboratory
Well-calibrated equipment is essential to guarantee quality in a laboratory. At SYNLAB Analytics & Services, Corina van Eijk deals with calibration processes almost daily. At WoTS, Van Eijk will talk about the challenges involved.
At SYNLAB, soil, water and air samples are tested for organic and inorganic environmental parameters. This can amount to 3000 samples per day. These samples are checked in SYNLAB's two accredited laboratories.
The amount of equipment that is eligible for calibration at SYNLAB is impressive: there are around 3500 devices in use, including 120 gas chromatographs, 6 electron microscopes and 10 HPLCs. But there are also pipettes, stoves, syringes and ovens.
Mutual differences
In her work as Manager QHSE, Procurement & Logistics at SYNLAB, Van Eijk tries to streamline the calibration processes in the various labs. However, despite European rules and standards, there are differences between member states: “We are accredited by the RVA. They have certain ideas about how to do that. The French Cofrac is stricter in calibrations for certain equipment. In Spain, we had an audit by ENAC. That organization has its own interpretations of how to deal with measurement uncertainties in a thermocouple. That makes it difficult, because you have different procedures that are not approved in other countries.”
According to Van Eijk, each country has its own focus when it comes to certification of calibrations: “The RVA has its own technical documents. Apparently, the ISO/IEC 17025 standard is not clear enough or is interpreted in different ways, because each country writes its own technical documents around it,” says Van Eijk.
On the work floor at SYNLAB, traceable calibration and checking are carried out, says Van Eijk: “You should not see calibration as an additional task in the production process, it should be part of the entire process. It is good if people perform the analyses themselves and also carry out the associated checks and calibrations. We use a specific schedule for all resources, such as the stoves and refrigerators.”
Digital control
The calibration procedures are controlled digitally as much as possible, but according to Van Eijk there are still procedures that can be improved: “We are faced with the fact that Excel sheets are still needed for some tasks. That is not always convenient. But if there are changes, you should at least communicate that clearly and possibly train people.”
During her presentation, Van Eijk will delve deeper into the challenges that come with calibration and controls at a large environmental laboratory. This not only involves the calibration of critical equipment and non-critical equipment, but also (sub)processes that can identify the greatest risks. And possible solutions can be surprisingly simple: “We also try to approach it lean by making it visual. Like a sticker on a pipette,” says Van Eijk.
Related companies
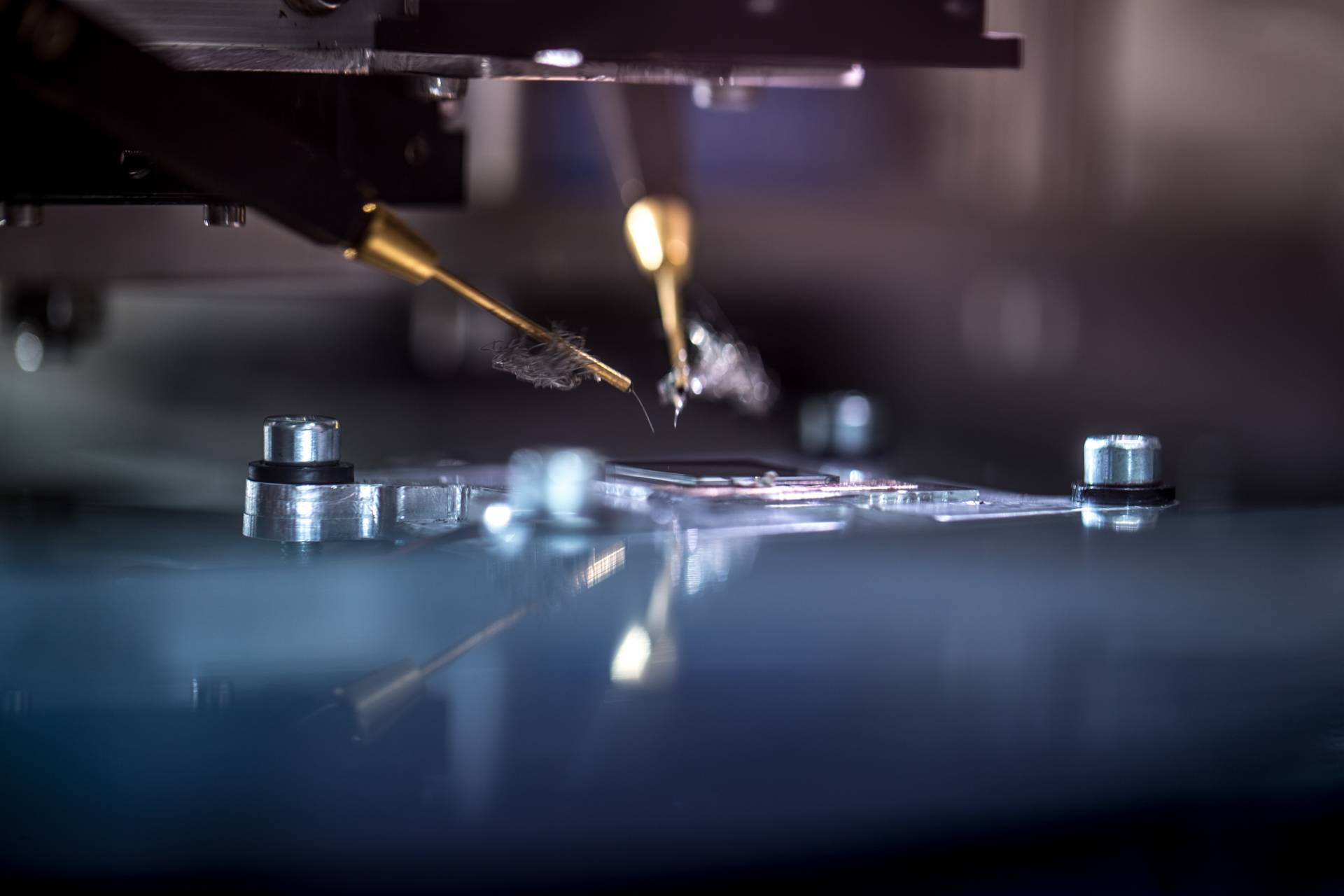
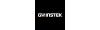