WoTS parrot takes flight: creation of the gadget
VDL TBP Electronics talks about the test phases
An electronic parrot is the trade fair gadget of the World of Technology & Science 2022. Behind the creation of the parrot – as the mascot is known in the corridors – there is a whole story. A team from various companies focused on the design, development and production of the gadget. In this interview series, the parties involved are discussed. In the fourth edition, Test Engineer Steven Van Hout of VDL TBP Electronics (stand no. 9C084) about his part in the project. He was responsible for the tests in the design phase and after production.
The role of VDL TBP Electronics within the project was twofold, says Van Hout: “In the preliminary phase, we made sure that we had sufficient space for testing. Before the design was finalized, we sent a test report to Dekimo sent. Our input was intended to ensure that the best and most suitable materials were used. Dekimo is at the heart of the gadget’s electronics. We also conduct tests before the gadget finally enters the production process.”
By thinking carefully about the materials to be used in the preliminary phase, you save a lot of time. During the Design for Manufacturing (DfM), it was examined whether the parrot was manufacturable and whether the desired electronics actually fit on the board. “For example, is it possible to solder in the current design and if so, which materials are most suitable for this? The goal was to prescribe an application that was as error-free as possible, so that the production process could be started as smoothly as possible.”
Assessing feasibility
The creation of the WoTS parrot is a real one team effort. Everyone involved helped each other to get the best out of the project and each other. “In consultation with the designers, you look for the best and most suitable components. Because the components have been well thought out, you prevent, for example, having to deal with scarcity. Because we received all the data at an early stage, we were able to perform an analysis in the preliminary phase to assess the feasibility of the design. We were also able to see whether additional hardware was needed for the tests. In the case of the parrot was that the placement of a loudspeaker, software and the implementation of LED lighting. The tests looked at what the blinking rate of the lights and whether the color intensity met the requirements,” said Van Hout.
A1 Electronics produces a total of 1500 parrots, each of which has been tested by engineers from VDL TBP Electronics. “We use our own test system, the EBST 2.0. We examine all the functionalities of the trade fair gadget. We also program firmware so that we can perform the tests properly. The tests are done both digitally and analogously. The entire board of the parrot undergoes a full Extended Boundary Scan test,” Van Hout explains.
Even more efficient
Fortunately, the testing process went smoothly. “We didn’t experience any problems or difficulties during the testing phase. At some point, we discovered that testing could be even more efficient if we captured both the USB and software in one test round. We did that separately at first, but when we discovered that we could bundle this, we did so immediately,” Van Hout concludes.
Name
Steven Van Hout
Organization
VDL TBP Electronics
Parrot project function
Responsible testing phases
Job description
Test Engineer
Related companies
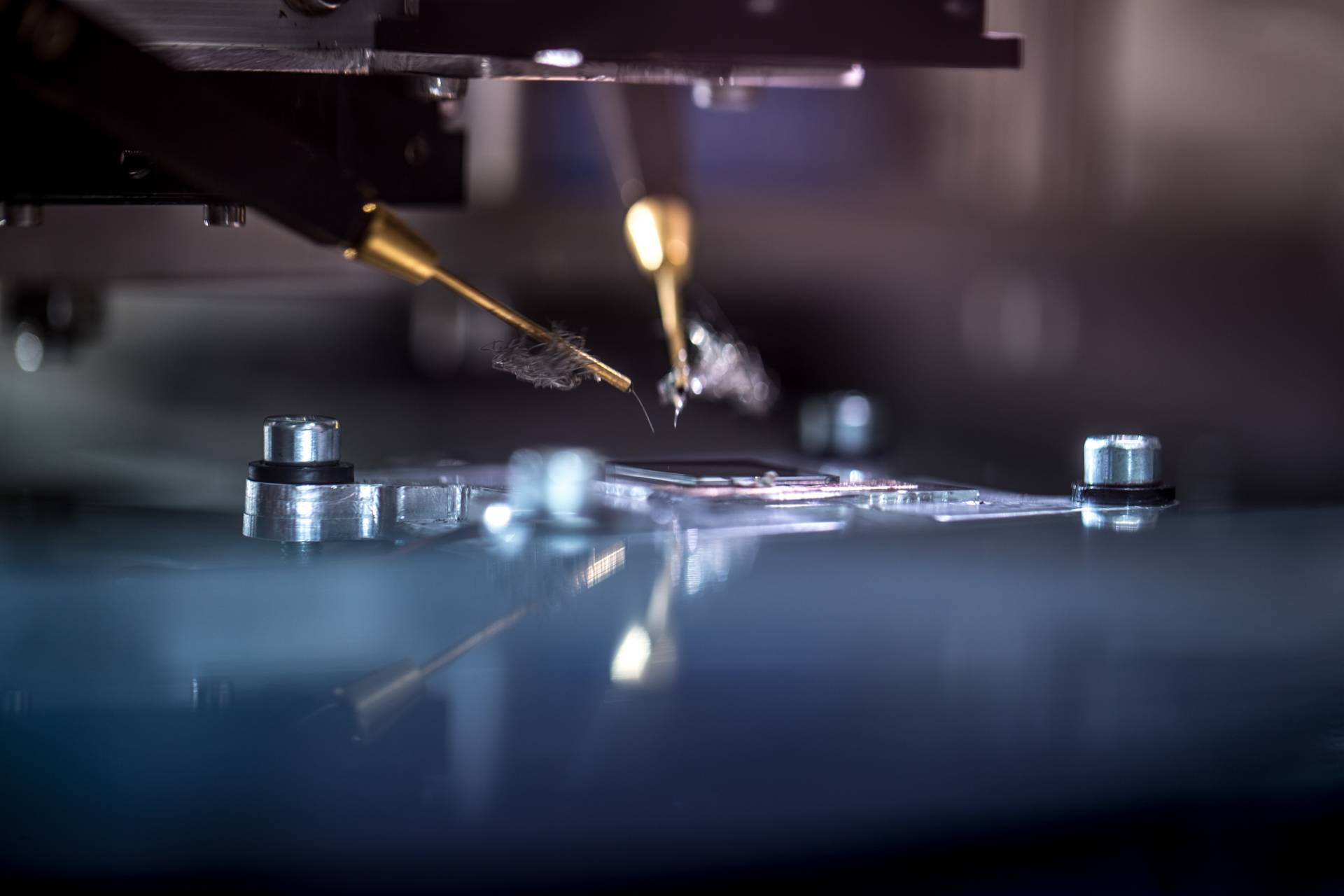
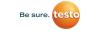