About machine communication and artificial intelligence: SMT sector is undergoing technological revolution
The Electronics & Applications fair is not complete without the production squareHere, visitors can marvel at demonstrations of working machines. There is also a production line where the trade fair gadgets are made. live are assembled. Visitors literally see how the PCBs of the HexaGlow gadget roll off the production line. Then they can assemble the interactive coaster themselves; a fun but challenging task that provides insight into the technology behind the gadget.
In the run-up to the fair, we spoke with Loek Sinke, service manager at Europe SMT in Turnhout, Belgium. Europe SMT is the exclusive distributor of Yamaha SMT machines within the Benelux and will facilitate the production line on the square to a large extent. “We keep it clear,” Sinke tells FHI. “The live line is equipped with a Yamaha YSP10 screen printer, a Yamaha YRM20R pick and place-machine with rotary head and a GoReflow 1.8 from SEHO, supplied by partner company KVMS. Also on our stand is the YRi-V AOI (automatic optical inspection) from Yamaha. On this machine we will demonstrate and visitors can see the latest technology of the AOI.''
Flexibility SMT line
Sinke: “The length of the assembly line at the fair is between eight and ten meters. That is relatively short. In our industry, machine setups of twenty to twenty-five meters are not at all unusual. Based on the customer's needs, we look at which machines are desirable. Budget, flexibility, speed and product specifications play an important role in this.”
Pick and place machine
An important part of the assembly line at the fair is the mounter, also known as pick and place machine. This last one is a good representation of what the machine does. Sinke: “The head in the machine ‘picks up’ the components and then places the parts on the PCB with very high precision. At top speed, this cannot be followed with the naked eye. After all components have been placed, the board (PCB) the next step in the process.”
The SMT process requires a streamlined approach with a high technical level. Sinke: “To create an efficient process, it is important that the process steps fit together well. Creating as many flow is a continuous process that requires a lot of attention. Translating machine data into usable operator-information is essential to make this process a success.” At the end of the line, the company places Smans a selective soldering machine (Ersa Versaflow One) to carefully solder the final component onto the PCB.
During the E&A fair, the software engineer from Europe SMT will provide a reading about machine-to-machine=communication of the latest generation of machines.
“The latest machines have the ability to work with increasingly smaller and more complex components. It is even possible to place components of 0.2 to 0.1 millimeters. This is so small that they are almost invisible to the naked eye,” Sinke explains. “The machines are also becoming faster and smarter. The YRM20 machine with rotary head can currently place up to 115,000 components per hour on a very small production surface.''
Just a few minutes
At the fair, this speed will not be achieved, because otherwise the PCBs will be ready within a few minutes. “At the fair, we will produce seven hundred and fifty gadgets, spread over three days, and of course we want to give the public the opportunity to view the process and ask questions,” says Sinke. According to him, it is 'typically Dutch' to produce smaller volumes and that is why the demand for flexible machines is high.
Future glasses
When Sinke puts on his future glasses, he sees that the influence of data-driven automation in PCB production is playing an increasingly important role. Sinke: “Developments are moving at breakneck speed. As a company, we always want to be at the forefront when it comes to new technological innovations. That is why Yamaha continuously invests in product and software development, which is necessary in the rapidly changing industry. Yamaha's latest platform enables machines to 'communicate' with each other in order to detect errors at an early stage and correct them themselves. Many printed circuit boards are also manually checked for errors, but with high production volumes that is no longer feasible. Moreover, our eyes are simply not capable of seeing components of 0.1 mm, let alone detecting errors. An AOI is a solution for this.”
Self-learning machines
Thanks to artificial intelligence in the machine, the Yamaha YRi-V AOI is self-learning. Sinke: “It works like this: if the operator approves the 'error' that the AOI machine signals, for example because the error falls within specification and does not affect the operation of the product, the AOI remembers this. The next time it will not report a similar error. The machine is therefore able to 'learn' based on artificial intelligence and to 'talk' to other machines.”
Great enthusiasm
Sinke expects that the production square at E&A will contribute to more insight into the far-reaching technological possibilities of modern SMT machines. “It is cool and educational to see what a production line looks like in practice.” According to Sinke, the collaboration with competitors towards the trade fair is going well. “The SMT industry is a fun sector to work in. Everyone is eager to show visitors what is possible in the technical field. Hopefully, that enthusiasm will rub off on the visitors to the trade fair. That is why we hope that students and job seekers will become interested in our sector after seeing the production square. Because although automation is increasing, we cannot do without well-trained professionals and great collaborations.”
Seize your chance
Can't wait to see an assembly line with your own eyes? Then grab your chance now and come to the Jaarbeurs in September. Register for the fair free of charge.
Related companies
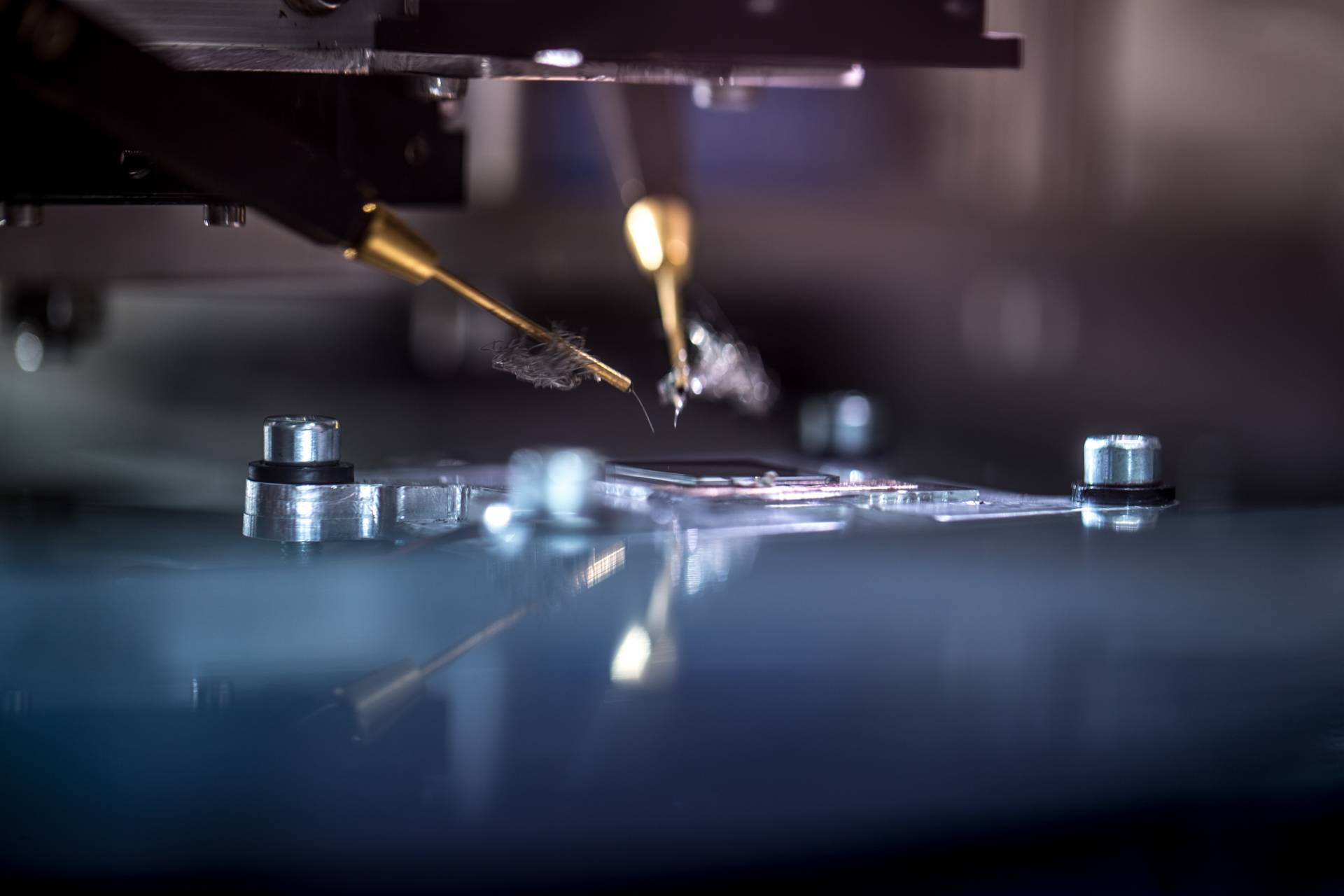
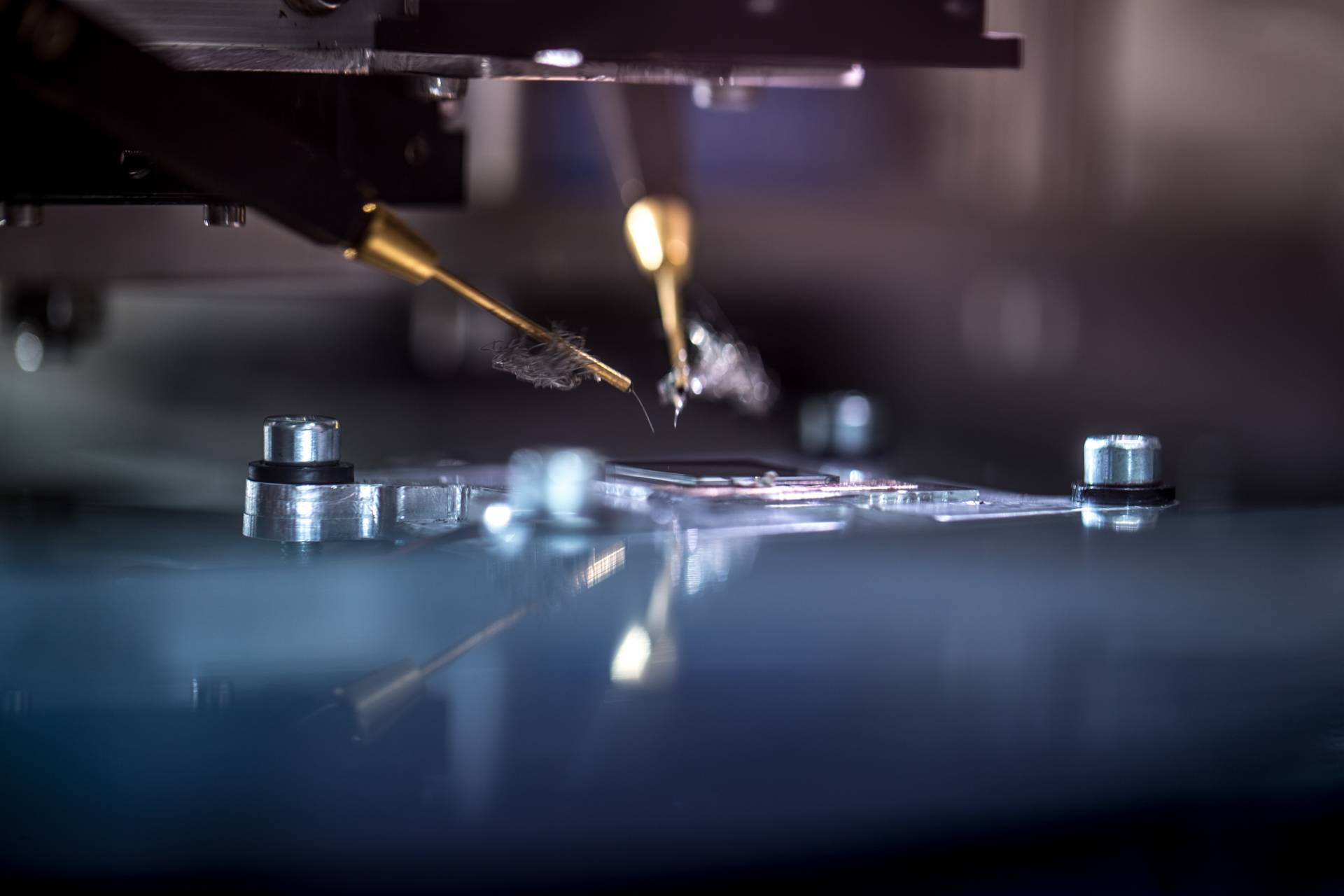
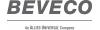